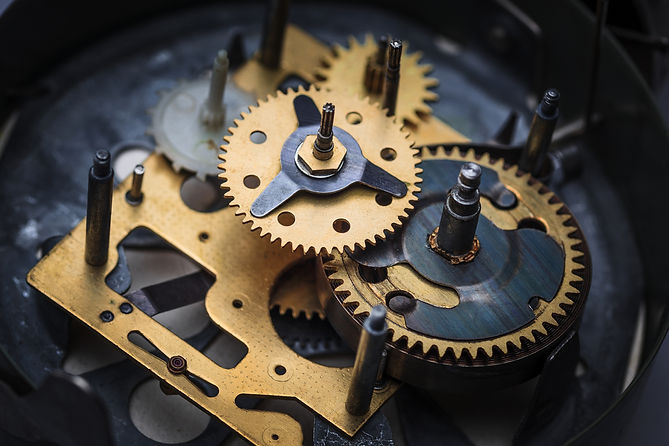
Mechanical Engineering
Mechanical engineering is a very broad field, including disciplines such as structural analysis, machine design, system dynamics & controls, fluid dynamics, and thermodynamics. Our engineers can design anything from entire medical devices to a single component of a larger device or system depending heavily on mechanical performance and reliability.
Research and Discovery Phase
The research and discovery phase of medical device design focuses on determining the requirements that provide the parameters for the design. We begin every project with research to understand the application requirements and select the best technologies to apply to meet them. Risks associated with the process must also be assessed at this point and communicated to the client. Another facet of this stage involves reviewing the FDA regulations and ISO specifications that would cover this device.
CAD (Computer-Aided Design) Engineering
With the System Architecture in place, engineers can begin developing the actual medical device design. Mechanical engineers are responsible for formulating all physical aspects of the device. They use both traditional design tools and modern 3D-CAD software to draft the shape and physical properties of the object. Raw materials are selected to meet the specifications, and the instrument design is separated into its constituent components. Throughout this stage, the engineers remain aware of the impact their design decisions will have on the manufacturing process and the project cost.
Prototyping
Once the engineering phase of the medical device design process has been completed, the next step involves the creation of a prototype. A prototype is a full-scale, working version of the design that is produced in limited quantities. We do have SLA/FDM 3D printing capability to produce prototypes more quickly and cost-effectively.
The prototype allows for the verification and validation of the device. Verification is the process of determining whether the specifications of the device have been met by the design process. Each aspect of the design - mechanical, electrical, and software - is tested. Validation, on the other hand, looks at the overall function of the instrument to ensure that its functions meet the needs of the client while conforming to all applicable international standards and FDA regulations.
Engineer Analysis
As the design matures, analyses are performed to verify the design. These include tolerance stack-ups, static, dynamic, and kinematic mechanical FEA (Finite Element Analysis), flow and thermal analyses, and optical studies as required for the design. Our mechanical engineers can build engineering analysis using tool such as mathematical modelling, computational fluid dynamics (CFD), Finite element analysis and tolerance analysis.
System Architecture
Next, we produce a design layout, incorporating top-level solutions to all identified requirements, and establishing the basic geometry, component interfaces, and construction of the device. Engineers create a definition for the device, including functional and structural relationships between components. Precision in the system architecture process is key to avoiding the need for potentially costly late-stage modifications to the project.
Material selection
Metals, ceramics, polymers, and composites are the most popular materials used for developing medical devices. These biomaterials must be non-toxic, non-carcinogenic, chemically inert, stable, and physically strong enough to withstand the forces imposed repeatedly over a lifetime. For fabricated components, we select materials fulfilling requirements such as impact strength, flammability, solvent resistance, and biocompatibility. We’re careful to respect fabrication process limitations (tolerances, surface finish, etc.) to assure the parts can be produced as designed.
Detailed design
Assemblies and parts are developed in SolidWorks, incorporating input from Industrial Design and the interface requirements of the purchased components. Oftentimes, components must be very tightly packaged, using cell phone design techniques to reduce overall size. Solutions are developed for issues such as EMC, ingress protection, rough handling, interconnects and routing, serviceability, and packaging.
Mechanical Testing
Mechanical testing is the testing of a material to find out its mechanical properties, for example, its yield strength or hardness. Throughout the design process, components, subsystems, and breadboards are tested to assure proper function, and during Design Verification, full systems undergo safety, compliance, and reliability testing.
DFMEA (Design failure mode and effect analysis)
DFMEA is a methodical approach used for identifying potential risks introduced in a new or changed design of a product/service. Our experience in designing and manufacturing a wide variety of devices means that our designs are easy to fabricate, assemble, and test. Mechanical engineers design for easy manufacture right from the start, we revisit manufacturability prior to release for Pilot Production review.